Neil Pollington, Operations Director at Severn Trent Green Power, talks about the company’s ongoing relationship with Komptech GB and how the key to its continued success lies in both the latest machinery and the continuous customer service that Komptech provides.
As one of the largest combined food waste recycler and composting business in the UK, Severn Trent Green Power (STGP) provides food waste recycling services to waste collection businesses and over 50 local authorities and turns half a million tonnes of organic waste into enough green energy to power 50,000 homes each year.
Komptech is an industry leader in supplying machinery and systems for the mechanical and mechanical-biological treatment of solid biomass as an energy source. STGP’s Operations Director Neil Pollington highlights this speciality as the initial driver for their partnership, as it provided an opportunity to move towards a more mechanical process.
“Komptech are the experts in green waste and IVC composting with equipment purpose-designed and built for these industries and applications. Rather than creating a machine that can do a bit of this and a bit of that. This felt like it was for the organics market,” Pollington explained.
“The fleet that we were operating [before] was ageing, and we were using quite a lot of manual intervention to remove contaminants.”
Komptech’s product range includes over 30 types of machines covering the critical process steps in modern waste handling, such as shredding, separation and biological treatment.
The partnership between the two companies began in 2018 when STGP initially bought the Hurrikan S, a mobile windsifter that removes light plastics, film and foils from screened overflow particles, with a separation efficiency of up to 95 per cent.
“Komptech provided an overview of what the machine could do. I had a look at the machine in their yard, and then they deployed it on a demonstration with us for a good period of time,” Pollington recalls. “I could see the value in the machine, what it was doing and how that would fit into the operation, how that would reduce cost and also improve contamination capture.”
STGP administered the Hurrikan S at their South Mimms site, a large IVC plant that has an annual throughput of up to 50,000 tons of primarily green waste that it receives from local authorities. “One of the other things that really surprised me is when we started to use the Hurrikan S, we got quite a bit of stone coming out of the process, quite a lot of metal being captured and obviously, a high level of plastic,” said Pollington.
The Hurrikan S allows STGP to have a segregated area for the sifting process with no crossover between people and machinery. It enables operators to screen any oversize contaminants and make the process safer, cleaner, and more efficient, giving Pollington the confidence to further invest in Komptech.
“I then purchased a second one for Ardley, which is our other in-vessel composting site, so basically replicated the same process,” said Pollington. “We just let it be for three months. We could see the real benefits and then rolled it out to the other site, which was positive. Then from there, we purchased two Crambo low-speed shredders.”
Komptech’s Crambo shredders are designed to process wood and green waste. Equipped with two slow-running drums designed to minimise fine particle, noise and dust emissions, the degree of shredding can be adjusted flexibly by exchanging its screen baskets. Komptech set up a demonstration of their Crambo 5200 Direct shredder at STGP’s Wallingford site. Pollington ran the current shredder against Komptech’s Crambo shredder to compare the output and decided to switch to the Crambo shredder after finding fuel savings and increased throughput hours with higher-end product yields.
“The biggest driver was the saving on fuel [and] the throughput per hour, as that saves operating hours,” Pollington said. “Previously, the high-speed shredder will be running all day to get the waste through the process where [the Crambo shredder] could now push it through in maybe five, six hours.”
“One of the other drivers was moving away from high-speed to slow-speed and making quite sure that you could shred the material without any contaminants in there being broken up too small, so they could be captured again by picking.”
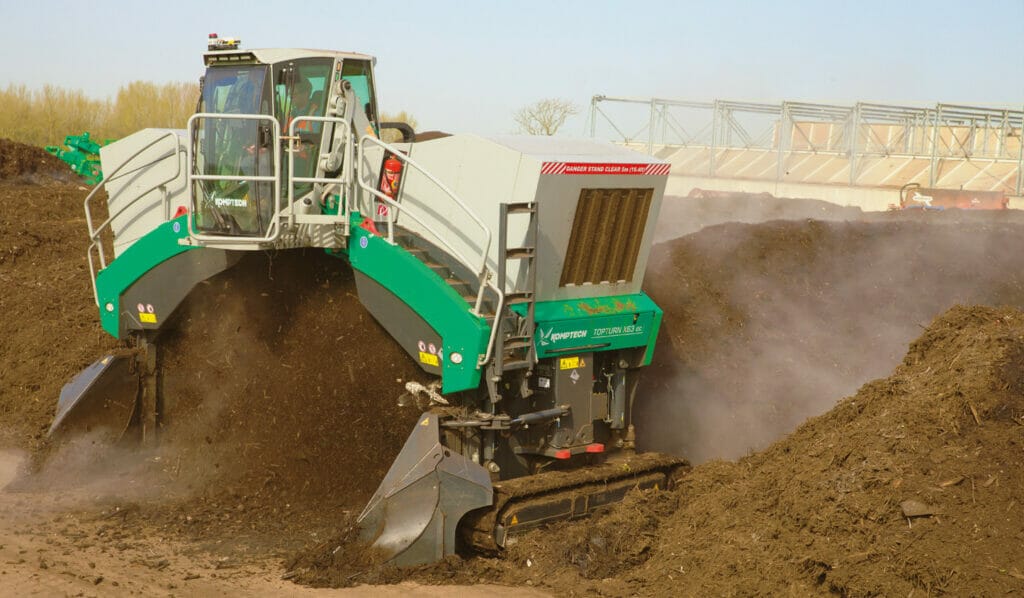
The Topturn X63 helped increase the windrow’s oxygen levels, break down the fine hair and increase fine compost yield.
STGP has also invested in Komptech’s Topturn X63 Track, a compost windrow turner that boasts an intake width of up to six meters and can achieve a turning capacity of 4500 cubic meters per hour. Upon its installation, Pollington recalls making sure it could fit into STGP’s operations.
“Again, Komptech organised the demonstration for us to see an X63 in operation on a composting site. We took several of the site managers to see that machine in operation and they were impressed with how it worked. It was as good, if not better than the machine that we were operating,” Pollington explained.
“I think the key thing to me was making sure that it could fit into our operation. Could it get over our windrows which are slightly bigger? We picked out a few large windrows on this other site, and they managed to get through it, and it seemed like it was going to be a good fit for our operation.”
The Topturn X63 has helped increase the windrow’s oxygen levels, break down the fine hair, and increase fine compost yield.
Since the implementation of Komptech’s product line, STGP identified an increase in odour control and reduction in odour complaints, something that the Environmental Agency also noted during site visits. The Komptech investment allows STGP to move from a manual based process to a more mechanical process, which has increased efficiency, reduced the need for manual picking and contributed to moving the composting process forward.
Another driving force behind the relationship’s success is Komptech’s commitment to providing after-sales coverage and training. Pollington recalls that as work with the initial Hurrikan S began, Komptech rolled out a training program for all operators at the South Mimms site, including full training criterion that STGP has since incorporated into their training plans.
“[Komptech GB] spent a lot of time with the team showing them the maintenance of the machine, how it should operate, how to set it up, how to get the best out of the machine. They were quite clear that it’s not a ‘tonnes machine’; it’s an ‘hours served machine’. It’s not how many tonnes you can get through. It’s the quality at the end,” explained Pollington.
As well as providing training to operators at STGP, Komptech GB has ensured their staff are always available to respond to any enquiries quickly. For Pollington, this support has been key for the continuation of the partnership.
“Komptech GB are very quick to react all the time. If the guys are struggling on-site, they’re on the phone to them. If I ask them to train six new guys on our machine, they will organise to do that,” Pollington said.
“The support has been the piece that gave me the confidence to continue with Komptech GB because they do support everything, and that’s the bit that gives me the confidence to keep purchasing and building the relationship with Komptech GB.”
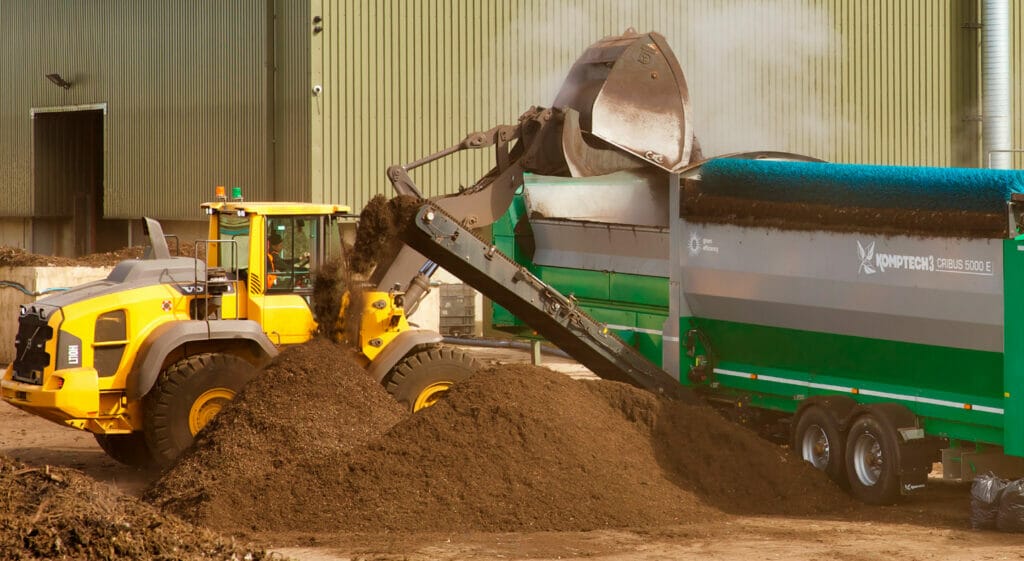
The hybrid electric drive Cribus 5000 has a 50cm screening area, operating with a high throughput.